Producer and transformer of plywood
Malvaux Marine has decades of experience in the use of plywood for the marine industry. The group is on the one hand a producer of plywood panels through its entity Malvaux Origin. It has a range of products, in marine plywood or CTBX, from various PEFC certified species TM and FSC ® it is a processor of wood, mainly poplar, birch, okoume and cheese. It is also a transformer via its Malvaux Manufactures factories (ex ST Bois, Naviline and Barbeau) which cut and machine wood, but also all types of non-ferrous materials. Its milling tools enable it to produce 3D parts for special elements of the boat, such as the bow or appendages.
Throughout the manufacturing of the plywood boat, Malvaux Marine accompanies its customers to optimize the assembly work and production costs.
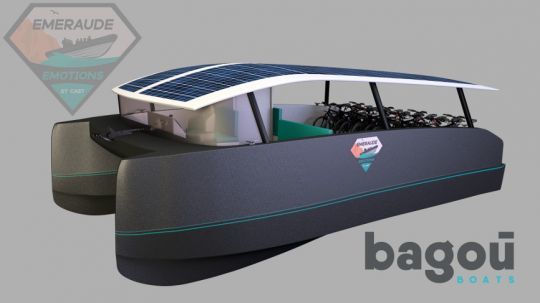
Supporting the design of the boat
The work begins when the files are received from the naval architect. The parts files are converted to be usable for the machines. "If necessary, we rework the files. We can also digitize plans from 3D or 2D surveys with our proliner, which can measure parts up to 10 meters in diameter. If necessary, we discuss with the construction site and the architect the thicknesses or the developability according to our experiences and the available panels. We may also discuss the quality of the plywood required, marine or not" explains Cyril Baudu, nautical business manager.
Designing the tooling
In many cases, the architects do not foresee the tools for the assembly of the boat. The specialists at Malvaux Marine then design the dummy that will allow the easy assembly of the boat's plywood couples. A construction site, cut out of 19 mm chipboard, is imagined to facilitate the work and the circulation of the operators, by anticipating the wedging of parts in 3D.
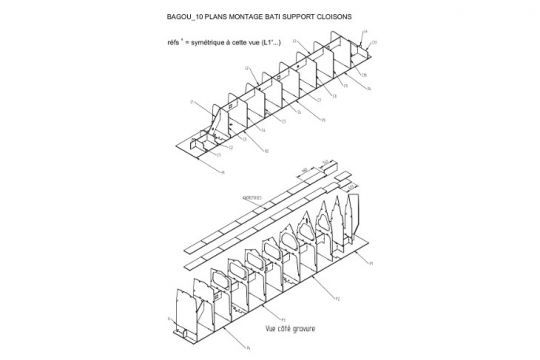
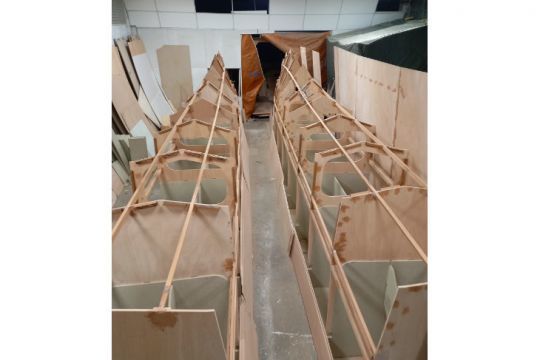
Digital scarf for edge assembly
Next comes the drawing of the digital scarves for the assembly of the large panels made in several parts. The layout of the joints, designed by the Malvaux Marine teams, is validated by the shipyard. "The digital scarf is as mechanically strong as the traditional scarf, but allows for both longitudinal and transverse wedging. Once validated, we adjust the tools to ensure that we have the right clearance for the parts to fit properly," explains Cyril Baudu.
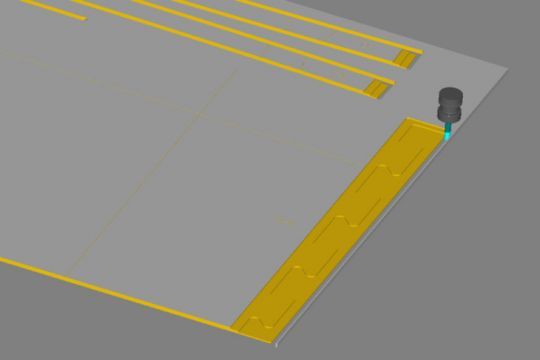
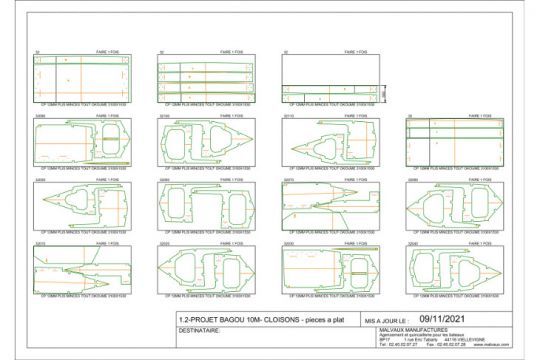
Cutting and shipping of the boat kit
Then comes the main step: the cutting of the panels. Once all the pieces are cut, the panels are reconstituted with the scraps for a better wedging in the transport and to avoid their damage. The scraps can be used for the realization of small parts and the wedging during the construction of the boat.
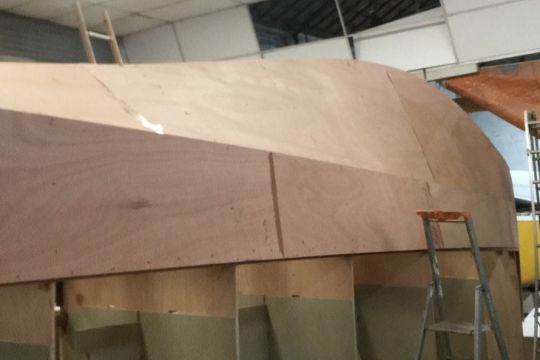
The kit is delivered with an assembly plan and a bill of materials. The assembly is then clear, and if needed, the Malvaux Marine team is available for explanations.