The disorganized world transport, not only for the nautical industry!
Logistics and supply issues have been crucial since the beginning of the Covid-19 pandemic. International trade has been severely disrupted, affecting product availability and pricing. "This is a supply issue that is not specific to the marine industry and it will be felt quickly by end customers. We work a lot with the United States, which has been very hard hit and disorganized due to the differences between states, with the added problem of transportation due to the storms. As the recovery has been faster in the USA, the flows are also tense for Europe because the local market is served first. There has also been an impact on Asia, which has put more sea freight into the US, with containers stuck there and a shortage of available containers, increasing the price of transport. A container that used to cost us between 3 and 4,000 euros was between 8 and 10,000 euros in December for the same 65 m3 of goods. In addition, the price of raw materials such as copper has increased by 30% or the zinc we use for our anodes. Suppliers are starting to want to increase their prices outside the calendar, which can only be a one-time thing," explains Benoît Massard-Combe, purchasing director for the marine equipment distributor VDM-Reya.
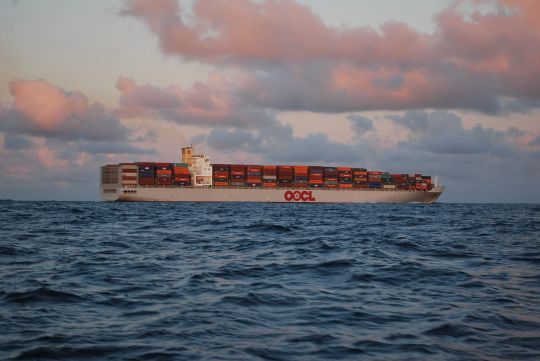
Anticipate the boating season
To ensure they have the products for boaters and limit the price spike, companies in the industry have adapted. "We saw the problem of restocking coming quickly because the aftermarket has picked up very quickly. Since September, we have been able to see that the impact on the original equipment of boats is also less than anticipated. Where we usually manage orders by quarter or even half-year, we sometimes placed annual orders last June to be sure of being served and having the products. We have noticed that with the breakdown of a single component in a country, such as the ceramic for our toilets in Sri Lanka, the delivery time could go from 3 to 6 months. So we did things in July, instead of the usual autumn," says Benoît Massard-Combe.
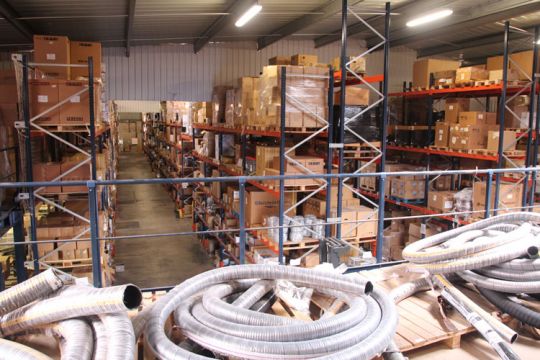
Thinking about the place of production of nautical equipment
If relocating the production of equipment in Europe is part of the solution, it cannot answer all the immediate problems, explains the purchasing manager of VDM-Reya in conclusion. "We are following the transportation costs and we are studying our referencing to stabilize the prices and to see if we can have certain products manufactured in Europe. But it's not always easy because there is a factory approval process that can be long, for example for safety equipment."